ABOUT
LOCATIONS
Strategically located across the United States and Mexico, Pace Industries has the largest footprint of any die caster in North America.
MATERIALS
The materials cast include a variety of aluminum, magnesium and zinc alloys to suit every application and mechanical properties.
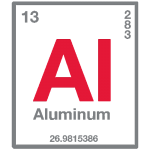
ALUMINUM
Pace has aluminum die casting machines ranging from 400 to 3,000 tons, giving us the ability to provide a large range of aluminum casting sizes and weights to serve nearly any industry and application. Aluminum die cast parts are lightweight, corrosion resistant and have a wide range of surface finishing options.
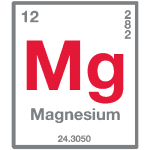
MAGNESIUM
Pace has extensive magnesium die casting knowledge and expertise, partnering with customers on the distinctive benefits of magnesium die casting to suit their needs. Magnesium offers a perfect combination of light weight, rigidity and resistance to wear for diverse die cast part applications.
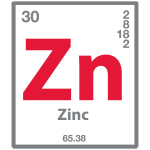
ZINC
Pace offers a variety of zinc die casting approaches that range from the ability to produce small, miniature zinc die castings to larger, conventional castings. Zinc provides unique advantages in many die casting applications that include a combination of strength, ductility, impact strength, finishing characteristics and tooling that has high resistance to catastrophic failure.
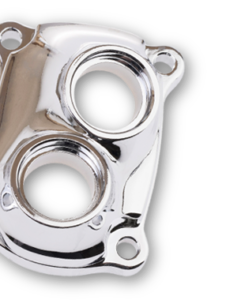
GET A QUOTE
Tell us about your upcoming project and our team will be in touch with you soon.
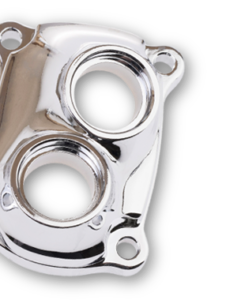
GET A QUOTE
Tell us about your upcoming project and our team will be in touch with you soon.